Our Client is a manufacturer of high-performance tires. During the manufacturing process, new tires must go through an internal wash before an absorbing acoustic foam is applied on them. As these tires are in production 24 hours a day, 6 days a week, water consumption is significant! The washing system consumes 500 liters of water per hour which represents 72 000 liters of water per week! It was therefore essential for our customer to use a treatment and wastewater recycling station which would be connected to this system. The clear water of the treatment would be returned in the system and reused.
Installation of a high-performance tire washing water treatment station
A wastewater treatment and recycling station was necessary for this high performance tire manufacturer that must proceed with internal washing of its tires during manufacturing, 24 hours a day, 6 days out of 7.
Goals and needs
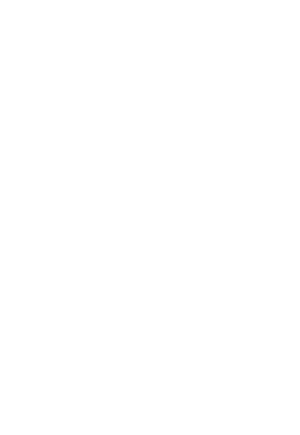
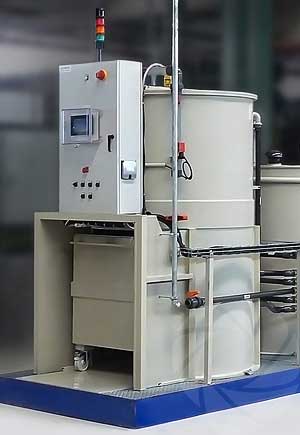
Solution
NISKAE has therefore installed an SW500 wastewater treatment and recycling station, with a 500 L/h capacity. This station which had been installed in of one our Client’s other plant in 2012, was recovered and refurbished. The whole installation has received a full upgrade by integrating the latest devices available on NISKAE’s wastewater treatment stations, such as: control panel, touch screen, web access, sludge sensors, motorized valves, level sensors, water meter, etc. Set on a compact platform equipped with a water retention pool, the station was relocated near the washing system.
How does it work ?
The wastewater is recovered in a tray under the washing system. Through a network of pipes, the wastewater is sent through a high temperature pump into a 1500 liters tank. It is equipped with an agitator in order to avoid the settling of suspended particles. The wastewater is redirected to the stations’ reactor with a pump and is then treated. The sludge removal is done in a filtration box placed under the reactor. The obtained clear water is accumulated in a 1500 liters tank and returned with a booster into the washing system. The washing of tires and wastewater recycling are therefore continuous and in a closed loop.
The treatment station is equipped with a touch screen control panel to follow each step of the treatment, the state of the station and the level of each tank. This panel is also equipped with an electrical outlet and a computer socket. Remote control is possible thanks to internet access. In addition, station status emails and statistical emails can be sent to stay informed on the entire treatment system.
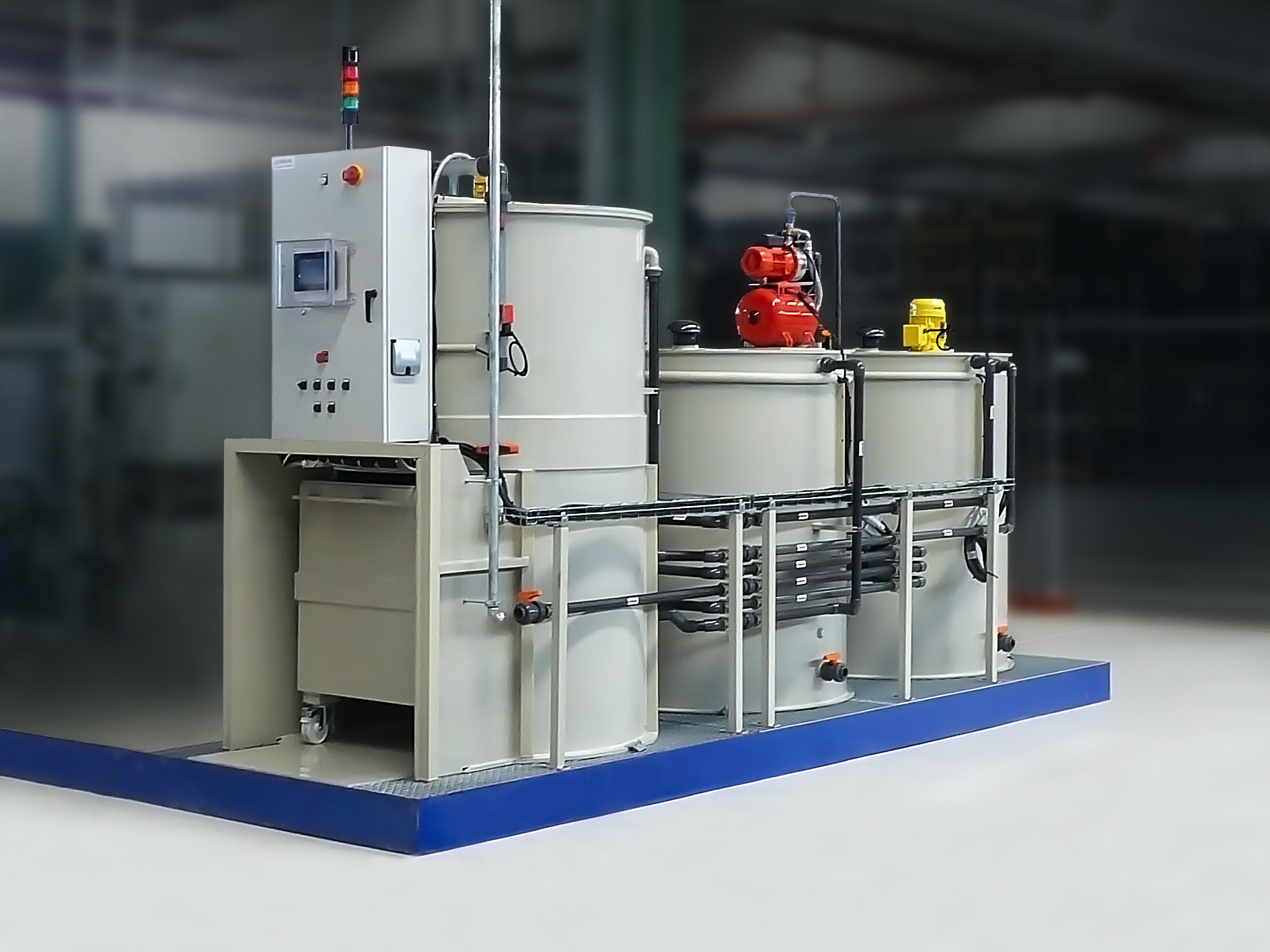
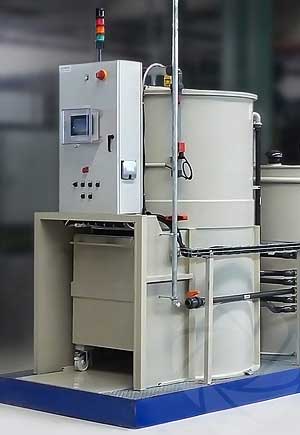
Results and advantages
-
Fully automated wastewater treatment and recycling system in a closed loop:
The same water is reused to wash the tires for a whole week.
-
Great water savings :
With the treatment station: 2000 liters of water are sent out for disposal each week.
Without the treatment station: 72,000 liters of water would be sent out for disposal each week.
-
No bulky tanks for storage of stagnant wastewater.
-
The treatment station and storage tanks are made of polypropylene:
A robust, durable and easy-to-clean material.
-
The treatment station, which was 4 years old, has been totally refurbished.
-
Each control panel is designed for a complete wastewater treatment system:
Additional options and upgrades are available after the initial acquisition of a basic treatment station.